To finish with this overview of the most widely used type of speaker, we'll discuss electrodynamic cone models. To improve the performance in the high frequencies, the cone is usually replaced with a dome, which is in turn placed in what's called a "compression driver," and attached to an acoustic horn to improve the coupling with the air.
Dome Diaphragm
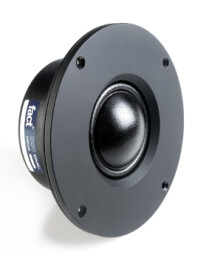
In generic terms, you could say that an electrodynamic dome speaker is a speaker whose diaphragm is of the same size as the coil. Visually speaking, the diaphragm occupies more or less the same place as the dustcap of a cone speaker. The materials used are more or less hard: coated textiles, composites and metals.
This design has some advantages for small speakers. It provides a solution to the displacement of the diaphragm in the highs and allows a larger dispersion angle in the high end. In other words, the hemispheric form of the diaphragm guarantees more rigidity and a less pronounced directivity of the highs. Moreover, the absence of a spider does away with some resonance issues.
Another benefit is that heat dissipation from the voice coil is much better because its diameter is maximal: it’s the same same size as the diaphragm. For example, with a dome tweeter that has a 1.57" (40mm) diameter, the voice coil would have a diameter of one third, about 0.51" (13mm). However, with a dome tweeter of the same dimensions, the voice coil would have a diameter of 1.57", providing a larger surface for heat dissipation. And then there’s the widespread use of ferrofluids ever since the 1970s. These viscose materials transfer the heat from the voice coil to the pole pieces, creating a thermal bridge that improves cooling.
Compression driver and acoustic horn
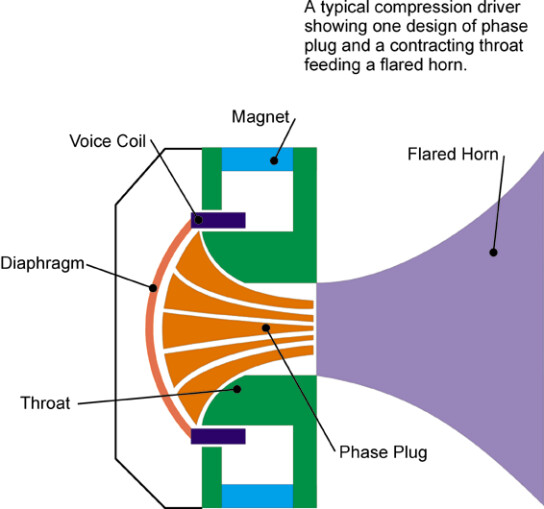
The first goal of the compression driver is to increase efficiency. On the inside is a dome diaphragm speaker whose diameter rarely exceeds four inches (10cm) This driver is coupled to an acoustic horn, which is basically a flaring duct. The narrow part of the horn is called the throat and the large part the mouth. It transforms large pressure variations on a small surface, near the diaphragm, into low pressure variations on a much larger area, near the mouth, which results in a better propagation into the air. Back in the 1930s, this allowed people to fill large rooms with sound.
The term “compression” comes from the fact that the throat is smaller than the diaphragm. The acoustic pressure is thus concentrated in the compression driver before being reproduced by the horn, guaranteeing a proper coupling to the air. This improves the sensitivity and directivity control.
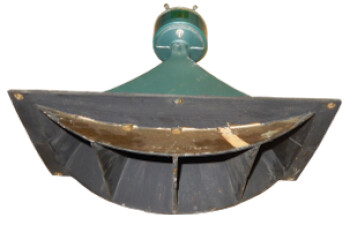
The coupling with the acoustic horn is achieved with a phase plug. The latter plays an important role in improving the sensitivity and the smoothness of the frequency response. It usually features concentric slots and is placed right above the diaphragm, leading to the throat of the horn. When it comes to acoustic horns, it’s interesting to review all existing profiles. They have been the subject of lots of research, in the quest for the best curve, and for a long time have helped in the pursuit of higher efficiency in sound reinforcement. Some progress has obviously been made, but the flip side is that the frequency response of acoustic horns has a tendency to be less linear than that of direct radiation drivers.
In subsequent articles, we’ll describe other models of electrodynamic speakers, starting with ribbon speakers.